
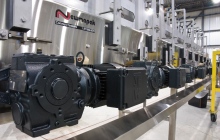
Photo by Pierre Longtin
If spotting new market niches and opportunities before the competition is what ultimately separates meaningful long-term corporate success from mere subsistence and survival, than the management of Newmapak Ltd.—Candiac, Que.-based conveying systems manufacturer and distributor—appears to have the formula for growth and longevity down to a science.
Founded in 1971, the company has established itself over the years as a well-respected manufacturer and designer of high-quality, reliable and durable conveying systems used to transport all sorts of packaging containers—full, empty, glass, plastic, etc.—through all the key production and packaging process stages, building up an impressive ‘Who’s Who’ list of clients that includes the likes of high-profile corporate heavyweights such as Patheon Inc., Wyeth (now part of Pfizer Inc.), Novapharm, ED Smith, Heinz, McCormick, Lassonde, Coca-Cola, Pepsi and Hiram Walker.
“We’ve been quite a successful company providing the services we provide, and have had a lot of repeat business,” says firm owner and president Robert Kucey, explaining that the company’s focus on providing clients with turnkey systems solutions for all their packaging application requirements has enabled the 15-employee company, operating in a state-of-the-art 20,000-square-foot production facility, to develop and maintain an extremely loyal customer base.
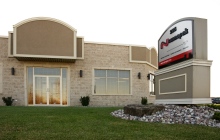
Photo by Pierre Longtin
“When we noticed a need for equipment integration services within the industry, we jumped at the chance to add that service to all the other things we offer,” says Kucey, relating the experience of Newmapak’s equipment installations in 2006, whereby after the Newmapak equipment was installed at the client’s site, the customer called in third-party electrical experts to hook up and wire all the systems and components to run as one smooth and cohesive line.
“That’s when we decided to add line integration capabilities to our portfolio,” Kucey told Canadian Packaging in a recent interview. “As such, we are willing, and are more than capable, to work alongside any other equipment supplier to design and develop the means to
integrate any machinery to ensure that our customer’s equipment will work efficiently.”
“Having a more balanced conveyor line is essential to helping them avoid bottlenecks, which besides the possibility of damaging their products could also cause a production line to be shut down,” notes Kucey. “And what company needs that headache?”
According to Kucey, proper conveyor systems integration is based on strategic positioning of sensors along the conveyor line to identify production flow problems as they unfold and send out messages via electronic relays to advise the motors that control the velocity of the
conveyor line whether they need to ramp up or ramp down their speeds accordingly.
“We’ll work with OEMs (original equipment manufacturers) to ensure that their machinery works in conjunction with all of our equipment,” point out Kucey, “so that the customer gets a production line that is always working at optimal efficiency.”
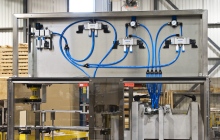
Photo by Pierre Longtin
While Kucey says that Newmapak likes to incorporate as much of its own equipment into turnkey lines whenever it makes sense to do so, its role as a systems integrator requires it to keep an open mind about systems made by other manufacturers as well, so that it can produce a truly ‘best-inbreed’ system solution for its clients.
To that end, Newmapak has gathered a fairly extensive stable of reputable OEMs whose machinery it recommends for virtually all key stages of a packaging line process, including:
unscramblers, rinsers, fillers, cappers, induction cap-sealers, labelers, caseformers, partition inserters, case-packers, case-sealers and palletizers.
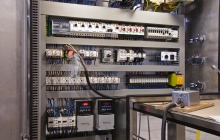
Photo by Pierre Longtin
Kucey stresses that regardless of whether a client purchases a completes turnkey production line comprising equipment from various manufacturers or a single piece of machinery, Newmapak is always ready to lend a hand to help integrate the equipment seamlessly into the customer’s existing production flow.
“We analyze a production line from start to finish and we can engineer for them a one-stop CSA-approved control panel or several control panels, if that’s what they desire, that we design and build on-site with our staff of mechanical and electrical engineers, to enable the customer to maintain better control of their production line,” explains Kucey.
“And we really believe that we are providing a much needed niche service,” Kucey stresses. “There are many companies out there that just sell the equipment, but we are one of the few in Canada to also offer the advantage of turnkey line integration.”
Kucey says that offering this advantage has played a crucial part in securing valuable repeat business from leading distilled spirits producers Hiram Walker, to use one of many examples.
Citing a recent challenging project at the distiller’s production facility in Windsor, Ont., Kucey recounts that the project involved removing a large part of an existing conveyor system— manufactured by a well-known material handling equipment supplier—and replacing it with a more flexible system that was better able to handle the flow of oval, flat, tapered and other irregular-shaped containers.
“Usually, irregular-shaped bottles have the potential to create a serious production problem bottle back-up pressure that occ
urs from shingling—when bottles run into each other and become stuck together,” Kucey relates.
“Essentially, we’re talking abut a real a production line nightmare that would involve having to stop a line to resolve the situation,” reveals Kucey. “Along with the time lost, there can also be a significant amount of damaged product, meaning real financial losses for the client.
“The solution we have devised for Hiram Walker will greatly minimize its occurrence and save them a lot of time, money and product,” says Kucey, adding that the new system is scheduled for startup at the Windsor facility in the early part of 2010.
Without getting deeply involved in the systems specifics for reasons of client confidentiality, Kucey says the new systems makes extensive use of various sequential motors manufactured by SEW-Eurodrive, one of Newmapak’s preferred suppliers, which it pre-wired into a single control panel that monitors all the data obtained by the different types of sensors set up along the line to tell the conveyor if and when it needs to adjust its velocity.
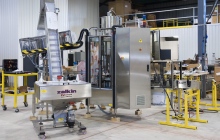
Photo by Pierre Longtin
“We essentially had a 12-week period during which we had to design, manufacture and test the new system,” says Kucey, adding that Newmapak also had to accommodate additional requests from the plant’s chief line mechanic after concluding the initial installation.
“But it was not a big problem for us,” Kucey recalls. “We listened, made same suggestions of our own, and completed all the modifications to the new system well within the additional two weeks we were given to complete the project.”
Giving the customers exactly what they want and need is an unwritten mantra at Newmapak, according to Kucey, who cites several other important technologies used in the successful startup and commissioning of the Hiram Walker project, including:
• The Allen-Bradley range of industrial automation controls and electronic devices from Rockwell-Automation, Inc.;
• The Telemecanique range of power distribution controls and systems supplied by Schneider Electric;
• Pneumatic devices—used for the lane gating mechanism of the new conveyor system—supplied by Festo Inc.;
• Omron controls and electronic components.
“For us, creating a rapport with all of our clients and trying to quickly find solutions for them is key to our success, Kucey reflects. “I believe that’s why we are able to generate a lot of repeat business—the clients wouldn’t be coming if we did not produce a decent product for them in the first place.
“But most importantly, we always aim to achieve 100-percent satisfaction for the customers,” sums up Kucey.
“When it comes to acting as a systems integrator, all of us equipment suppliers need to forget about being competitors and concentrate on working together to find a mutual solution that will make the customer happy.
“That just makes good business for everybody involved.”
Advertisement
