
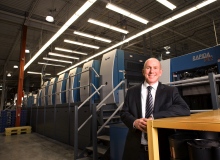
Photo by John Hrynik
If spending money is a key pre-requisite for making more money down the road, then there are some very exciting years just up ahead for Boehmer Box LP—a historical institution in Canada’s folding-carton industry and one of its largest players, with virtually unmatched market reach and plenty of pent-up production capacity just waiting to be unleashed.
Founded way back in 1874 under the A&C Boehmer moniker in Kitchener, Ont., the 125-year-old folding carton producer today ranks as one of the country’s three largest manufacturers of high-quality paperbox packaging products for brand-owners and private-label customers in the food-and-beverage, pharmaceutical, personal-care and other high-profile CPG (consumer packaged goods) industries—producing an estimated 700 million litho-printed packages last year at its sprawling, 320,000-square-foot Kitchener facility.
Today operating as part of the CanamPac ULC group of packaging companies—also comprising the Strathcona Paper LP paperboard mill in Napanee, Ont., and a newly-formed independent affiliate LYFT Visual, a provider of pre-media services and printed marketing products to retailers, CPG companies, product manufacturers and ad agencies—Boehmer managed not only to post double-digit growth during the recent economic downturn, according to company president and chief executive Mark Caines, but also embarked on an extensive, $10-million capital investment program that firmly entrenches the company at the forefront of the Canadian industry’s technological leadership.
“Our goal is to be producing one billion packages at our Kitchener plant in coming years,” Caines told Canadian Packaging in a recent interview, pointing out that the 270-employee Boehmer plant is currently operating at only about 70 per cent of its total output capacity, despite running a busy four-shift, 24/7 schedule throughout most of the year, with a day or two off for Christmas.
“We have experienced sales growth of about 20 per cent in the last year and we expect another 15-percent increase in the coming year,” says long-time printing industry veteran Caines, who joined Boehmer in September of 2005 to steer the company on a course of continuous improvement and investment in next-generation printing and converting technologies to support the projected production growth.
“We are now the largest producer of primary packaging for the private-label brands of Sobey’s, Loblaws, Walmart, Metro and most other main retailers, with about a 50-percent share of the Canadian private-label business, serving our clients coast-to-coast right across Canada,” says Caines, adding that the Boehmer plant had created over 40 new full-time jobs in the last year to keep up with growing production levels.
“Don’t get me wrong, the Canadian folding-carton industry is an extremely tough place to make a buck—it is highly competitive and the margins are very small,” points out Caines.
“But we really believe that we can achieve our growth targets and objectives through a combination of our highly-efficient manufacturing processes, high product quality, fast turnaround times, and continued investment into world-class printing press technologies.”
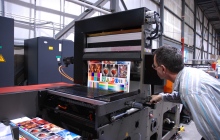
Photo by John Hrynik
PRESS TO IMPRESS
Manufactured in Germany, the recently-installed KBA model Rapida 142 six-color, 56-inch press—supplied by KBA North America’s Canadian distributor KBR Graphics Ltd.—accounts for a large portion of Boehmer’s $10-million investment spree, Caines relates.
“Our reputation has been built on investing in new technology to differentiate us from our competitors,” says Caines, adding the new, UV-prepped KBA press will make a perfect production complement to the Kitchener plant’s existing MAN Roland six-color, 56-inch offset press and the six-color, 50-inch sheetfed press from Mitsubishi.
“Our new Rapida 142 press is an essential part of the investment,” Caines asserts. “We needed a new press that would provide the automation, fast make-ready, color fidelity, and ability to easily integrate with our robust prepress department, as well as our unique FM6 expanded color printing technology.
“Our plan is to run this press to capacity where it will be operating 24/7 along with our existing 56-inch press,” he expands.
“We’ll be much more efficient in make-ready and turnaround times because our new KBA press is running 45-percent faster than the press it is replacing,” says Caines, complimenting its robust operating speeds of up to 15,000 sheets per hour, as well as full compatibility with the proprietary, extended-gamut FM6 six-color process technology, licensed from the Belgian-based PrinTech Systems B.V., which enables the matching of a broad range of specific brand colors in a single pass without having to load special inks.
“Color and graphics are very important to our customers,” says Caines, “which is why in 2006 we invested in the patented FM6 technology—making us the only printer in North America to be using this process, which reproduces the traditional Pantone spot color library in a single printing pass using CMYK, FM orange, FM blue and FM green.
“Due to this technology, we’re able to put 10 or 15 different boxes on one sheet and hit the color gamut for each customer,” he relates. “In fact, FM6 has become so popular that nearly 80 to 85 per cent of our customers now ask for it.
“In order to run it properly, we needed a press like the KBA Rapida 142, which has the required color and density control technology.”
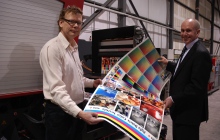
Photo by John Hrynik
Called Densitronic Pro, this proprietary, combined density-and-color measuring system is designed to permit direct measurements within the image both during and after printing, according to KBA, quickly displaying any deviations from target densities, color values, and other qua
lity parameters such as dot gain, trapping, etc.
With integration for online control, the density and spectral deviations are converted into corrective adjustments for the individual ink keys, with the Densitronic Pro system automatically controlling the density and spectral parameters of each sheet by measuring along control strips or directly on the image—at far greater speeds than with the traditional hand-held measuring devices.
Combined with the Rapida 142 unit’s fully-automatic and simultaneous plate-changing capabilities for vastly reduced make-readies, “This installation is the best press startup I have experienced in my 25 years in the printing industry,” Caines enthuses.
While the high-output Rapida 142 press may be the Boehmer plant’s newest workhorse, the newly-acquired digital Dotrix press—manufactured in Belgium by AGFA Graphics—is more of a rare-breed, multi-trick show pony geared for flexible, short-run production of cartons, high-end labels, posters, product samples, and various promotional and test-marketing kits.
Installed about three months ago around the same time as the Rapida 142 press, the digital press has “already been getting great feedback from our customers,” says Caines, praising its unparalleled flexibility that allows for the customization of each and every carton or other product being processed during the actual print run.
“This is just about the most high-tech printing technology out there right now,” says Caines, adding that the Dotrix installation has enabled CanamPac to establish the new LIFT Visual digital printing and pre-media unit, headed by himself and industry veteran Serge Traikovich.
WORK TO DO
“It’s a very new technology, so we have some work ahead to develop the market,” Caines admits, “but in terms of final print quality, the results we’ve been getting have already exceeded our expectations.
“There is definitely a trend in the marketplace towards a higher frequency of graphic changes on the package and a reduction in length runs,” says Caines, “and the Dotrix digital printing process is exactly what we needed to capitalize on this trend.
“Being a digital press, and having no printing plates, allows us to be very cost-effective on short runs with a high level of graphic changes,” he explains, “and it allows us to run jobs requiring variable data.
“The press is also capable of running essentially any substrate that can be purchased on a roll—from plastic to paperboard,” Caines points out. “We can also run it roll-to-roll or roll-to-sheet, as required.
“I think that it will take a little time for the digital printing process to become more mainstream, mainly because of the high cost of the inks and consumables,” he allows, “but these costs are offset by less waste, less plates, etc.
“We are happy to embrace this technology right now because it accurately represents the future evolution of package printing technology, while also allowing us to support the marketing efforts of our customers.”
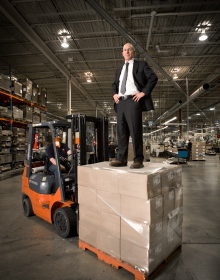
Photo by John Hrynik
All in all, Caines says he is highly satisfied with the performance, quality, flexibility and the high level of process automation that the two new presses have enabled the Boehmer plant to achieve in the relatively short time since their installation, concluding that the company’s extensive capital investment—also including the purchase of a rebuilt 56-inch Bobst die-cutter and next-generation prepress technologies from ESKO Graphics—will prove its worth with a healthy ROI (return-on-investment) in coming years.
“Just a couple of weeks ago, we performed a complete product changeover on the new KBA press in under 18 minutes,” he extols, “whereas it would’ve taken us an hour or more on the old press that it replaced.
“For a company like ours, which produces more than 3,000 SKUs (stock-keeping units), such flexibility and agility is a priceless asset that will serve us well into the future, as we continue to grow and consolidate our marketplace gains.”
Advertisement
