

Photo by Pierre Longtin
Doing a job well the first time around is undoubtedly a key prerequisite for making that all-important good first impression on a new client, but it’s the ability to deliver the goods time after time that often separates contenders from pretenders in today’s fiercely competitive global marketplace for pharmaceutical co-packing and contract manufacturing services.
For Confab Laboratories Inc., a 30-year-old, privately-owned drugs and pharmaceuticals co-packer based in Saint-Hubert, Que., getting things right for its customers is an everyday quest that is consistently approached with the mindset of doing whatever it takes, whatever the effort and cost, to keep its customers coming back.

Photo by Pierre Longtin
According to Confab’s director of costing and regulatory affairs Dominic Lamarre, such commitment to customer service excellence has been one of key drivers behind the company’s impressive growth since its founding in 1979 by his father Guy Lamarre, company chairman and chief executive officer, along two other current principal shareholders—general manager Nathalie Brisson and vice-president of operations Denis Church.
“The manufacturing of drugs is a multibillion-dollar industry, and for us to work in such a heavily regulated market, we must always ensure that we do things correctly,” Lamarre told Canadian Packaging in a recent interview.

Photo by Pierre Longtin
Strategically located near the Canada-U.S. border, the company employs 285 highly-trained personnel at a modern, state-of-the-art, 140,000-square-foot facility that produces and packages a plethora of tablets, capsules, liquid doses, syrups, suspensions, suppositories, ampoules, creams, lotions and ointments for a broad range of human and veterinary healthcare providers, while offering range of services that include product and process development, analytical and stability studies, and third-party validation.
GLOBAL REACH
Serving a fairly diverse international client base—comprising customers in 15 countries across five continents—Confab counts some of the world’s leading OTC (over-the-counter) and prescription drug companies, generic drug manufacturers, and nutraceuticals producers among its highly valued clientele.
“While the majority of our annual production is geared for the North American-based clients, about 15 per cent of our output is shipped to our European, African, Australian and Asian customers,” says Lamarre, pointing out that the company’s strict adherence to the internationally recognized C-GMP (Current Good Manufacturing Practices) protocol requirements enables it to pursue new business opportunities overseas.

Photo by Pierre Longtin
According to Lamarre, one of the company’s biggest growth spurts occurred in 2001 with an extensive, $4-million facility expansion that involved installing six independent ventilation systems for air conditioning and heating—including a 30/30 type of filtration—that are checked both visually and via magnehelic meters by a computerized system that controls the differential pressure, humidity and temperature in each of the plant’s 70 separate cleanrooms.
“We also added a dust collection system that helps minimize the chance of crosscontamination during the manufacturing and packaging of the various products,” recalls Lamarre. “It’s been a key factor for us, as a third-party manufacturing and packaging provider, that Confab always
needs to watch its turnaround times, which is why we are always improving our state-of-the-art facility and constantly investing in the best production equipment on the market.
“It’s the only way to keep ahead of the competition.”
About four years ago, continues Lamarre, the company decided to upgrade its packaging capabilities as part of a plan to offer true turnkey capabilities to its clients under one roof.
“We realized that if we could combine the product testing and manufacturing with the packaging,” he explains, “we would be able to better control the product quality, pricing and lead-times. It only made sense that by being a ‘one-stop shop’ for our customers, we could ultimately provide a better product at a reasonable cost.”
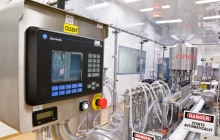
Photo by Pierre Longtin
As part of that upgrade, Confab invested into a high-performance Patriot FC 21 multistation monoblock system—including a filler and a capper for processing 15- to 250-ml bottles—supplied by the Montreal-based packaging systems manufacturer and integrator Capmatic Ltd.
Having been sufficiently impressed with the system’s performance since its arrival in 2006, Lamarre says he had no misgivings about going back to Capmatic again last year, when a major new customer order proved to be a little beyond the plant’s existing packaging capabilities.
“In 2008, a client of ours asked us to increase, in fact to nearly double, the annual volume of a multi-unit package we were manufacturing and packaging on another line,” Lamarre recounts. “Not wanting to let the customer down, we decided that purchasing another production line would be a prudent investment.
“So we sought out Capmatic again,” says Lamarre, explaini
ng that this particular job required for the secondary packaging paperboard carton to contain a capped and labeled vial/bottle with a tamper evident neckband, a pre-sealed liquid application dropper, and a folded paper insert with all the instructions on how to use it—with Confab not only producing the product itself, but all the components as well.

Photo by Pierre Longtin
To meet Confab’s strict application requirements, Capmatic responded with a prompt delivery and installation of the turnkey Conquest Pharma line configuration—integrated with a model Sortstar empty bottle unscrambler—designed as a multiple-station, continuous-motion vial filling-and-capping monoblock system, developed specifically for pharmaceutical industry applications.
“Although it may on the surface appear to be a simple filling, capping and packaging line,” Lamarre notes, “with Capmatic’s help we have made it full of numerous safety detection devices that will ensure not only a top-notch product for our clients, but one that will not sacrifice production flow for us.”
Featuring Capmatic’s seal-less, cam-driven PharmaValve piston pump technology, the Conquest Pharma can fill and cap vials at speeds up to 200-bpm (bottles per minute) with ±0.5-percent filling accuracy, according to Capmatic, with its proprietary CompufillAllen-Bradley PanelView 600 software and an electronic operator interface from Rockwell Automation facilitating smooth programming and process monitoring, as well as high-precision dispensing of the drug.
Designed specifically for filling operations in aseptic environments, the Conquest Pharma also features an eight-head, rotary continuous-motion flow bottle/vial filler and aluminum vial rotating cap crimper, programmed to match the filler’s operating speeds of 120 vials per minute.

Photo by Pierre Longtin
STAR TURN
Designed as a starwheel system, the high-speed crimper is equipped with a vial sensor on the infeed section to halt the process if a bottle is missing or misaligned, while the starwheel’s outfeed is outfitted with a pair of Omron machine vision cameras and a pneumatic Festo ‘rejector’ mechanism to detect and remove any product rejects that haven’t been capped properly.
After capping, the vials are moved through a Capmatic banding machine and on to a heat tunnel that applies a tamper-evident plastic layer over the cap and down to the shoulder of the vial, with a Banner UV (ultraviolet) sensor used to confirm the presence and positioning of the neckband seal.
The vials then pass through a Capmatic LabelStar to attach the product label to the vial, after which a newly installed Markem-Imaje small-character heat-transfer printer completes the label by instantly adding all the relevant lot and expiry date information.
Next, an Optel Vision label inspection camera system checks individual labels to ensure proper readability and positioning of the just-printed label data, with a second Festo ‘rejector’ device ready to spring into action to remove any product with incomplete information or improper label placement.
“From there,” Lamarre notes, “the now finished vials continue along the horseshoe-shaped line to meet up with the pre-sealed liquid dropper applicator, which is where the robotic systems come into play.”
Employing a Cognex camera machine vision to track and relay the positioning of each vial as it moves down the packaging line, the FlexPicker pick-and-place system from ABB utilizes a pair of robotic arms to pick up the dropper applicators off the conveyor belting in a swift and gentle motion—with each arm capable of about 150 picks per minute—and place them into the tray containing the vial.
After this step, a made-in-Germany Guk leaflet dispenser adds a pre-folded paper information/instruction
sheet, and the fully-assembled kit is moved on to the Flexa horizontal intermittent high-speed cartoner—capable of reaching speeds of up to 200 cartons per minute—manufactured in Italy by IMA.
After the Flexa places all the product components inside the passing carton, a Systech vision system confirms the presence of the components; an Eclipse Series pattern control system from Nordson generates a seal on the top and bottom flaps of each carton; a Lasetec laser-based coder from Fumex prints lot and expiry date information of the bottom of the cartons; and another Systech camera verifies the integrity of the seal and the presence of all the required printed data.

Photo by Pierre Longtin
While Lamarre notes that Confab has only started the process of performance validation for the new Capmatic line, he says everyone has been impressed with what they have seen so far.
“Despite the number of pieces of equipment contained within this line, we are very pleased its compact footprint and how it seems to be working,” says Lamarre, adding that Capmatic capably met all of Confab’s strict performance and space requirements with this installation.
“Because each of our packaging rooms has a highly technical air quality system—which is quite expensive to construct—the packaging rooms are generally quite small,” he explains. “As a result, we needed to have a fast and efficient packaging line that can work within a small footprint—and that’s exactly what we received.
“So in the end,” Copping concludes, “opting to purchase another Capmatic line was really not that difficult a choice for us.”
Advertisement
